1. Increase Quality and Process Efficiencies
Notable Outcomes:
-
.....
-
....
-
.....
-
......
-
.......
-
.........
Under Construction
Utilize Lean + 6s tools to foster a culture of continuous improvement by organizing the workplace, eliminating waste, and enhancing productivity. Tis practical systematic approach ensures sustained efficiency, quality, and employee engagement, ultimately driving long-term business success


Prioritize continuous improvement initiatives using a practical tracking tool that evaluates projects based on their alignment with strategic goals, ease of implementation, return on investment (ROI), resourcing requirement, and the potential to mitigate compliance and safety risks. This structured approach ensures that resources are focused on initiatives that deliver the greatest value while supporting long-term operational objectives. Inputs into the tool include annual site goals, ideas generated from dedicated new idea meetings, and performance insights from the KPI scorecard
Lean 6s Training and Certification utilizing blend of internal and external programs with focus on 'Learning', 'Applying', 'Leading'. This also includes lunchtime tool learning sessions, and focused development in investigation capabilities. This approach ensures employees gain practical skills, drive continuous improvement, and strengthen problem-solving for operational excellence.
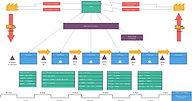
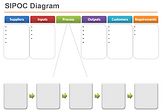



Value Stream Mapping (VSM) is a powerful tool for process improvement, enabling organizations to visualize and enhance their workflows from end to end. By calculating Process Efficiency (Value Added Time/Total Time), VSM helps identify areas of waste and opportunities for optimization. It's recommended to start with a SIPOC (Suppliers, Inputs, Process, Outputs, and Customers) analysis to outline the macro-level process. This sets the stage for a detailed VSM, providing a comprehensive view of the entire process, highlighting value-added and non-value-added activities. By leveraging VSM in conjunction with SIPOC, organizations can create a holistic process map that drives efficiency, enhances quality, and fosters continuous improvement.
Utilization of industry-proven tools in practical problem-solving (e.g., Kepner-Tregoe, Pathwise, 8D, Apollo). These methodologies enhance critical thinking and RCCA capabilities. Most problem-solving methodologies are rooted in long-standing quality tools such as the IS-IS NOT matrix, Fishbone Diagram, 5 Whys, Process Mapping, and Hypothesis Testing. Leveraging these foundational tools ensures a robust and systematic approach to problem-solving, enabling effective identification and resolution of root causes. By integrating these methodologies and tools into training programs, it will build and strengthen critical thinking and RCCA capabilities, fostering a culture of continuous improvement and operational excellence.